
Saving money is top of mind for manufacturers who want to boost their bottom line. Yet, many overlook opportunities for cost-savings in their own production facilities. This article will explore various strategies, such as lean manufacturing and automation, that can lead to significant savings in your plant operations.
Get ready to revolutionize your approach towards optimizing operational costs!
Key Takeaways
Making less waste saves money. Factories can do this with lean manufacturing and good supply chain management.
New technology helps cut costs too. Robots take care of boring tasks. Smart tech catches mistakes early.
Workers should be well - trained and happy at work. This makes them faster, smarter and more careful.
Saving power is another way to save cash. Using energy-saving tools or led lights can help a lot.
Adopting Lean Manufacturing Principles for Cost Savings
Embracing lean manufacturing principles is a valuable strategy for cost-cutting in manufacturing, focused on identifying and eradicating wasteful procedures to optimize production flow.
The Toyota Production System (TPS) serves as an excellent benchmark, detailing methods such as Waste Reduction, Value Stream Mapping, 5S, Total Productive Maintenance, Just-In-Time (JIT) manufacturing, and Kaizen.
These practices target the elimination of overproduction waste as well as minimization of inventory-related costs all with the endgame to boost the profitability of your business by transforming your status quo into a streamlined and highly efficient operation.
Reducing waste
Cutting down waste helps save costs. Here is how to do it:
Go paperless. Use computer systems not paper. This will cut down waste.
Use electronic work instructions. This helps lower the number of mistakes made during work.
Handle waste well. Waste comes from making things. If not handled right, it can be costly.
Use IoT technologies in Industry 4.0 to watch product quality and find issues early on.
Make the workplace safe and healthy for workers to avoid waste from accidents.
Use sensor - enabled wearables that can collect data on safety at work.
Take care of supply chain management well to lessen waste by avoiding too much or too little inventory.
Reuse and recycle materials as much as you can instead of throwing them away immediately after use.
Implement quality control systems to avoid producing flawed products, which means less material wasted.
Optimizing production flow
Improving how things get made can save money. Here is how:
Use lean manufacturing principles. These cut waste and make production better.
Put in electronic work instructions. This can help lessen mistakes, make more items, make choices better, cut the time to teach staff, and fill skill gaps.
Add IoT technologies from Industry 4.0. They can watch the quality of goods, find faults, and lower bad output.
Check out smart Factory technologies. They give up-to-the-minute details for top-notch supply chain management.
Save on energy costs with new technology and gear that doesn't use much energy.
Stop machine failures with predictive maintenance to avoid unplanned stoppages.
Enhancing Labor Efficiency

Manufacturers can enhance labor efficiency by focusing on staff training and development. It's crucial to equip employees with the necessary skills and knowledge to perform tasks efficiently.
Moreover, a high level of worker engagement improves productivity and reduces errors, saving costs in the long run. The efficient use of labour not only promotes cost savings but also improves product quality and customer satisfaction.
Training and development
Good training helps workers do their jobs well. Training programs can teach many things, like how to use tools, follow safety rules or make work better. It also saves time and resources.
New trends, technologies and the best ways to work are taught too.
Workers feel good when they get a chance to learn more. They feel happy about their job and want to do it better. This makes them work faster and smarter. Some plants have unique needs or problems that need special training courses.
Employee engagement
Happy workers help a plant run better. When workers are involved, they work harder. This can mean fewer mistakes and less waste. Also, these workers often have ideas to make things better.
Employee engagement helps see and fix skills gaps in the workforce too. Using tools like digital transformation or digital marketing can make a worker's job easier and increase their engagement at work.
So, caring for your staff is key to saving costs in a company!
Implementing Cost-effective Automation Solutions
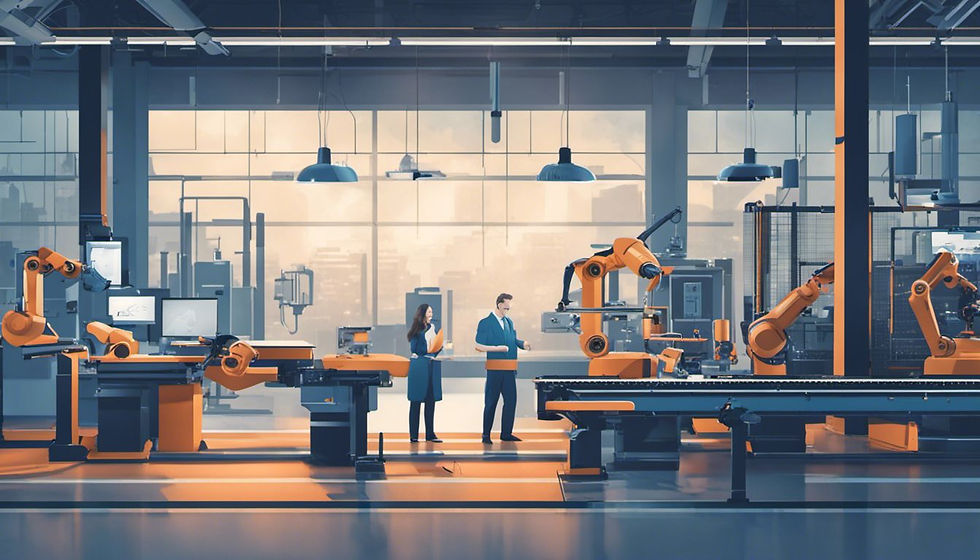
The competitive landscape of manufacturing demands the implementation of cost-effective automation solutions. By automating repetitive manual tasks, efficiency can be markedly improved and human errors minimized.
Smart manufacturing technologies such as robotics, artificial intelligence, and machine learning provide valuable tools for enhancing productivity while reducing labor costs. A detailed cost-benefit analysis helps to identify the most advantageous areas to automate and ensure a good return on investment.
Investing in automated solutions not only drives down costs but can also become a key driver of growth and competitiveness in today's fast-paced industrial environment.
Automating repetitive manual processes
The use of automation can cut costs in manufacturing plants. It brings many benefits:
It takes over dull tasks. Workers then focus on complex duties.
Robots do not make errors like humans do.
They work 24/7 and don't need breaks, sick days or vacations.
Damage from mishaps drops when machines take over.
Robots use fewer resources like electricity.
Utilizing smart manufacturing technologies
Smart manufacturing technologies can help cut costs.
Try digitizing your workforce. It may reduce costs and boost productivity.
Use electronic work instructions. They can lower mistakes, raise output, speed up decisions, save training time, and help fill skill gaps.
Try IoT technologies in Industry 4.0. You can keep an eye on product quality; you can find faults and bring down faulty output.
Use tech like sensor - enabled wearables and data analysis to make the workplace safer.
Inventory-related decisions can be better with real-time data from smart technology.
Automate repetitive manual tasks to save time for more important work.
Track key performance indicators (KPIs) with AI upgrades for better insights into your operations.
AI, robotics, machine learning are good cost-effective automation solutions.
Negotiation skills will be useful in getting raw materials at a lower cost from suppliers.
Use Deloitte Analytics or VKS Lite to check equipment uptime and automate manual processes to save labor hours.
Decide production volume by keeping tabs on the market fluctuations using real - time data from smart technology.
Streamlining Supply Chain Management

Efficient coordination of the supply chain and implementation of inventory management can significantly reduce costs. By leveraging smart technology, real-time data becomes available for making informed, cost-saving decisions related to inventory.
By applying effective negotiation skills in obtaining raw materials, freight costs can be prepaid with favorable financing terms.
Coordinating supply chain
Coordinating the supply chain can cut costs. Good coordination makes sure you have just what you need. It keeps you from buying too much. When you buy too much, you waste money on storage. This is called carrying cost. Also, having extra supply can lead to waste if things go bad or become old.
Implementing inventory management
Making use of inventory management helps manufacturing plants control costs. It lets them follow how much stock they have. This can help save money in many ways:
It can cut down carrying costs tied to extra supply.
Better watch on stock means fewer times when items run out or are overstocked.
Using smart technology and software improves the accuracy of inventory management.
Forecasting demand and order quantities become simpler.
Just-In-Time inventory practices become possible, cutting down wastage.
Optimizing Energy Efficiency
Manufacturing plants can greatly reduce operational costs by focusing on optimizing energy efficiency, incorporating energy-saving technologies and initiatives to limit waste. They can invest in smart thermostats, LED lighting, and energy-efficient equipment.
Regular audits of utility bills help identify areas for improvement while contributing to a reduced carbon footprint. Government subsidies may also be available when implementing new protocols aimed at decreasing overall energy usage within the facility.
Ultimately, cutting down on unnecessary power consumption not only leads to significant cost savings but also promotes more sustainable manufacturing practices.
Implementing energy-saving technology
Factories save a lot of money with energy-saving technology. Manufacturing plants use these steps:
Replace old lights with LED lights. They are brighter and use less power.
Use smart thermostats to control the heat and cold in the building. These devices save energy by only heating or cooling when necessary.
Install energy - efficient tools and machines. They do the same work but use less power.
Monitor your factory's carbon footprint. Factories that harm the environment less might get money from the government.
Set up new rules about how to save energy on the assembly line.
Reducing energy waste
Manufacturers often lose money on wasted energy. Here are some ways they can cut those costs down:
Use digital tools: Going paperless can help plants save costs and be more green.
Install smart technology: Stuff like IoT devices can optimize energy use in the plant.
Make work safer: Sensor-enabled wearables and data analysis can limit risky behavior.that wastes energy.
Update old gear: Using energy-efficient equipment will lower power bills.in a big way.
Get an audit: A utility audit can spot areas where your plant is wasting too much power.
Optimize lighting: Switching to LED lights can cut down on a plant's energy use.
Install smart thermostats: This allows for better control over heating and cooling, which reduces waste.
Keep machines running well: Regular check-ups prevent breakdowns that cause extra power usage.
Upgrading and Retrofitting Equipment
Regular checks of factory equipment are critical to ensure optimal performance. By investing in proactive, preventive maintenance, manufacturers can detect issues early before they cause expensive breakdowns.
Upgrading aging machinery with modern technology not only enhances efficiency but also reduces repair costs. Retrofitting existing machines can improve their productivity and lifespan, providing substantial cost savings while keeping the environment safe by reducing waste.
Proactive preventive maintenance
Proactive preventive maintenance is an important step to cut costs in any manufacturing plant. It holds a lot of benefits:
Stops major problems: Regular checks can find issues before they turn big. This stops costly fixes and delays in work.
Cuts down on sudden repairs: Good maintenance lessens the chance of sudden machine breaks. This saves time and money, as you won't need fast, pricy fixes.
Boosts efficiency: Keeping machines in good condition means they can run better and faster. So, you get more work done with the same amount of time and resources.
It's a smart move: Proactive measures are always one step ahead. They spot risks before things go wrong. You do not wait for a problem to pop up but make sure it does not happen at all.
Regular equipment checks
Making sure equipment is working right is key in a manufacturing plant. Regular equipment checks hold many benefits.
They help find small problems before they become big ones.
These checks stop machines from breaking down when you need them most.
Less downtime means work keeps going and money keeps coming in.
Workers stay safe because faulty equipment gets fixed fast.
You can plan for future needs by knowing how well your gear is doing.
It can lead to savings because things run smoothly and efficiently.
This process goes hand-in-hand with upgrading and retrofitting equipment, adding to cost savings even more.
Reducing Material Waste
Manufacturing plants can significantly cut costs by reducing material waste, a step that involves reusing and recycling materials whenever possible. By implementing strict quality control and assurance processes, industries can minimize the amount of wasted materials, thereby saving resources.
Reduction in material waste not only saves money but also aligns with sustainable and environmentally-friendly business practices.
Reusing and recycling materials
Reusing and recycling materials helps to cut down on waste in manufacturing plants. Here are some ideas:
Start a recycling program. Use bins for paper, plastic and metal.
Reuse items like boxes, padding, and packaging.
Check used materials before throwing them away. They might be reusable.
Think about how you can use less material in the first place.
Make sure everyone knows about the recycling program.
Try to find ways to reuse things that seem like waste.
Use recycled materials in your products if you can.
Quality control and assurance processes
Quality control and assurance processes are key to cut down material waste. These tools make sure all goods meet set standards. This can catch any mistakes before they become big problems.
It lowers the chance that bad products will be made.
Using this method, plants save money by using fewer materials. They also lower costs because there are less faulty goods to fix or throw away. In addition, customers get better items which build trust in the brand and product over time.
Consolidating Product Offerings
A cost-saving strategy for manufacturers is consolidating product offerings, which involves executing a product-line rationalization to identify less profitable products and focus resources on high-demand items.
Through strategic product development, companies can refine their offerings by improving existing products or introducing new ones that align better with market needs. This consolidation process not only reduces manufacturing costs but also boosts profit margins by focusing on the most lucrative segments of the market.
Product-line rationalization
Product-line rationalization helps manufacturers focus on their best products. These are the steps to a successful product-line rationalization:
Look at all your goods.
Pick the ones that sell the most.
Make less of the items that do not sell well.
Stop making some goods if needed.
Strategic product development
Strategic product development is important for any manufacturing plant. This process works in a few steps:
Look at each product's profits. Think about how many you sell and the price you sell them at.
Check if some of your products sell more than others.
Use this to decide what products need work or can be let go.
Make sure to get energy - saving lights, heaters and coolers.
Train workers on how to save energy.
Work with other companies who make the same things as you do to share good ideas for saving energy.
Be aware of how much waste your plant makes and create a plan to reduce it.
Find ways to cut back on waste special to your plant.
Understand that cutting waste is important in making new products better for everyone involved.
Optimizing Facility Layout and Design
Efficient facility layout and design are crucial for manufacturing plants to ensure smooth operations. A well-designed workspace boosts productivity, reduces waste, and enhances safety standards.
It decreases travel time between different processes, leading to quicker turnaround times. Furthermore, a safe and healthy working environment is critical in reducing workplace injuries, improving the overall morale of workforce’s health & safety measures.
Therefore, optimizing your facilities' designs can result in significant cost savings.
Efficient workspace design
Good workspace design saves money. It helps workers do their jobs better and faster. Easy to move around areas are key. So is making sure tools and materials are in the right place.
Plan out work areas so that people have enough space. This helps avoid accidents and makes sure work gets done fast.
Keep tools in places that make sense. Workers should not have to waste time looking for what they need.
Use good lighting everywhere. This helps workers see their tasks clearly and avoid mistakes.
Make sure there is air flow and it's at the right temperature. If the air is too hot, cold, or stuffy, workers can get tired or sick.
Design areas to cut down on noise. Too much noise can hurt ears and make it hard to think.
Use colors that are easy on the eyes. Bold colors can distract, while soft ones help focus.
Safe and healthy working environment
A good working space is safe and healthy. It helps to stop workers from getting sick or hurt. This means less time off work and lower costs for insurance. The right order of tasks, placement of machines, keeping areas separate and safe help keep the workspace healthy.
Wearables with sensors can track safety data too. They point out risks so you can fix them before anyone gets hurt.
Outsourcing Non-Core Manufacturing Activities
Outsourcing is a great way for factories to save money. It lets them give tasks they don't specialize in to other firms. This can improve how well the work gets done and lower costs too.
Many plants choose to outsource tasks like cleaning, security, or IT.
It's also common to outsource making parts that aren't central to what the factory makes. The firm saves time and resources because it focuses on its main job: creating its product.
It then spends less money trying to do everything itself which helps increase profits.
Developing Strategic Partnerships
Manufacturing plants can gain significant cost savings by developing strategic partnerships. Strengthening ties with chosen suppliers, for instance, can lead to bulk-buy discounts and preferential delivery terms.
Collaborations in product development or shared marketing efforts with other businesses can also spread the costs while increasing market reach. These alliances not only provide financial benefits but also foster innovation and growth opportunities within the manufacturing industry.
Supplier partnerships
Making good bonds with suppliers can save a lot of money. These partnerships open the door for many benefits.
Buying raw materials at lower rates is possible. This brings down costs.
Suppliers often give better terms to their partners. This could mean less money up front or longer to pay.
They help to make sure enough goods are ready when they are needed. This cuts extra supply and carrying costs.
Together, manufacturing plants and suppliers can find new ways to be energy efficient. Partnerships like this lead to new ideas that help both sides.
Trusted suppliers can act fast in changing markets. This keeps things running smoothly even when times are tough.
You might get to try new products or services before others do if you have a strong bond with your supplier.
You may also get better service from your supplier if you share a close relationship.
Collaborations for product development
Working together for product development is a smart move. It saves money for plants that make things.
Teams can join hands to think up new products.
Ideas from different people can make goods better.
Trying out new ideas can lead to cost cuts and more sales.
Shared problem - solving leads to faster, cheaper solutions.
Working with others helps find the best ways to make things.
It's good to learn from other companies' wins and mistakes.
Strong bonds formed during teamwork can be useful in future projects.
Utilizing Tax Incentives and Government Programs
Tax cuts help plants save money. For example, tax credits, exemptions and fast asset depreciation ease the tax burden. The IRS website gives a lot of helpful details about these benefits.
Grants and low-interest loans from the government also boost plants' performance. These might be for training or other resources that keep a plant running well. Manufacturers can find many programs that suit their needs.
To get the most out of these perks, factories have to take certain steps. They must review their records often and make sure they are correct. Plus, they should think about how these incentives fit with other ways they fund their business.
Conclusion
Adopt new ways to save money at your plant. Use digital tools and train workers. Make less waste and keep workers safe. Save energy, work smart, and see big savings!
FAQs
1. How can manufacturing plants save costs?
Manufacturing plants can cut production costs by using cost savings consultants, doing utility and telecommunication audits and optimizing business practices such as reducing waste.
2. Can digitizing the workforce help in cost reduction?
Yes, digitizing your workforce can reduce labor shortages, fill skill gaps and cut down on labor costs through automating repetitive manual tasks.
3. Does workplace safety affect cost saving?
Yes! A safe workplace reduces insurance claims from on-the-job illness or injury which lowers absenteeism rate thereby saving money.
4. Why is energy efficiency important for manufacturing plants' financial health?
Using energy-efficient equipment helps to cut energy costs in heating, cooling and lighting while qualifying for some government subsidies that boost a plant's financial health.
5. How does preventive maintenance affect my company’s bottom line?
Preventive measures like regular equipment check-ups help avoid unplanned downtime which cuts down on machine downtime costs thus boosting your profits.
6.How can 'Standardization' save me money?
Through Standardization good manufacturing practices are enforced leading to lower defect density rates hence fewer customer returns - this directly saves you money.